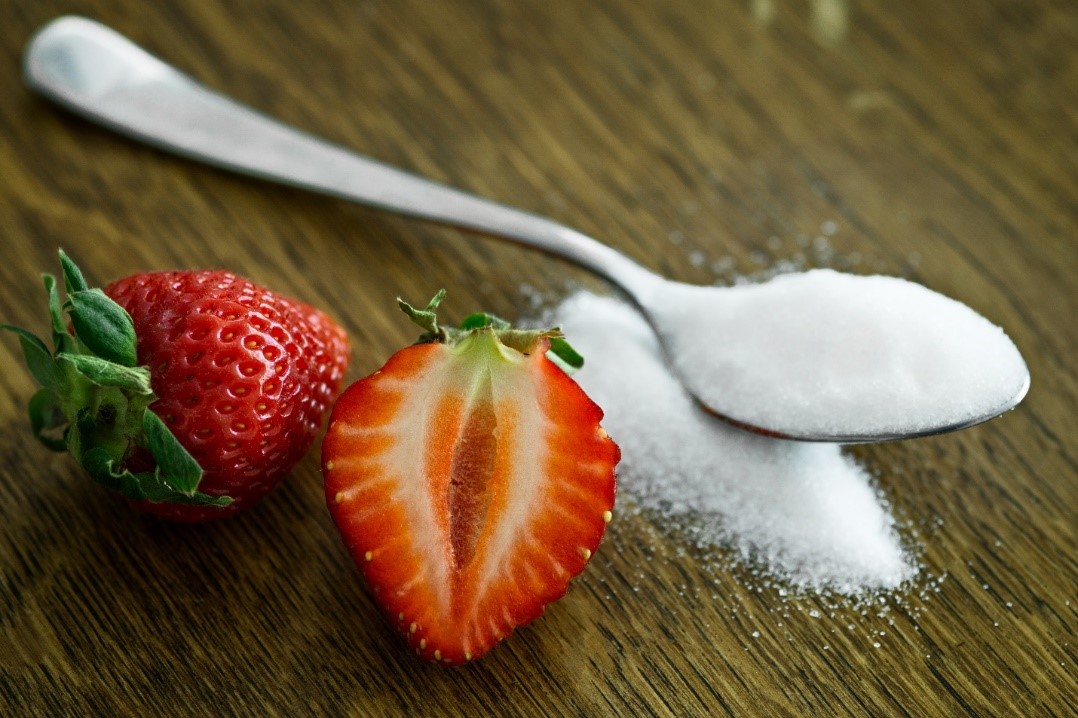
A Tate & Lyle é um dos líderes globais no setor de alimentos e bebidas. Isso é comprovado por um histórico longo e impressionante de “fazer alimentos extraordinários” ao transformar milho, tapioca e outros materiais brutos em ingredientes que adicionam sabor, textura e nutrientes aos alimentos. Um dos produtos mais conhecidos nos EUA é o adoçante sucralose SPLENDA®.
Quando enfrentou um desafio no processo de refino de açúcares de milho, a Tate & Lyle procurou a ajuda do software Minitab.
O Desafio: Uniformizar o tamanho da partícula de cristalização
Quando Adam Russell começou a trabalhar como Master Black Belt de Operações Globais na Tate & Lyle, ele recebeu um desafio: Uniformizar o tamanho da partícula dos açúcares de milho.
“Um dos recursos cruciais para qualidade de um processo de cristalização é a distribuição do tamanho da partícula”, diz Russell. “Por que isso é tão importante? Bom, quando desenvolvemos esses produtos para consumidores, 20 a 30 anos atrás, eles queriam que os açúcares de milho tivessem o mesmo gosto e textura do açúcar refinado ou de cana de açúcar. Você precisa atingir uma certa distribuição do tamanho da partícula para que isso aconteça.”
A Tate & Lyle estava com problemas, pois essas partículas estavam ficando fora do intervalo aceitável, e eles não conseguiam identificar o motivo. A empresa tinha uma lista de fatores mantidos tradicionalmente e determinou que isso afetava a variação do tamanho da partícula:
- Temperaturas
- Pressões
- Taxas de fluxo
- pH
- Condutividade
E a lista continua.
Como o Minitab ajudou
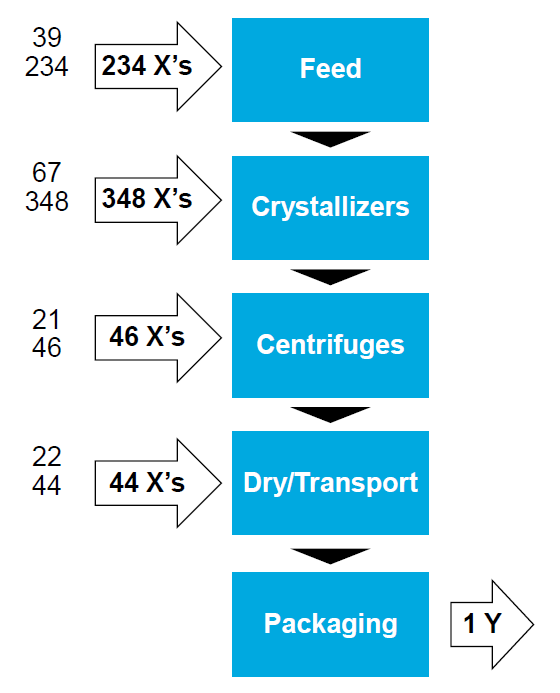
Uma versão simplificada do mapa de processo que a Tate & Lyle criou no Companion by Minitab (agora Minitab Engage®). No processo de cristalização de açúcar de milho, o xarope é recebido de uma refinaria e depois cristalizado (o que leva muitos dias), depois centrifugado, secado e colocado em pacotes para os clientes.
Eles começaram a usar o Companion by Minitab (agora Minitab Engage®) para criar um mapa de processo que mostrou uma visualização geral do processo de cristalização (saiba mais sobre mapas de processo). Eles não estavam atingindo uma distribuição do tamanho da partícula confiável, então queriam compreender o que estava causando a variação e como controlá-la.
“Tudo é medido em uma fábrica química”, disse Russell. “Cada ponto possível tem um transmissor que está fornecendo informações de volta ao historiador de dados. Isso é excelente, mas cria o desafio de termos muitas informações e não sabermos o que fazer com elas.”
Para compreender visualmente os dados de tamanho de partícula, Russell e sua equipe usaram o Minitab Statistical Software para criar a carta Xbarra mostrada abaixo.
Muitas das relações entre as variáveis eram não lineares, por isso, ficou difícil identificar o impacto que uma tinha na outra. Além disso, o tamanho de partícula é desconhecido até que seja colocado no pacote para os clientes, pois está no estágio de secagem em forma de gel, entre líquido e sólido.
Há mais de 1.000 possíveis entradas em um modelo como esse. Apenas modelos de regressão múltipla não levam a respostas.
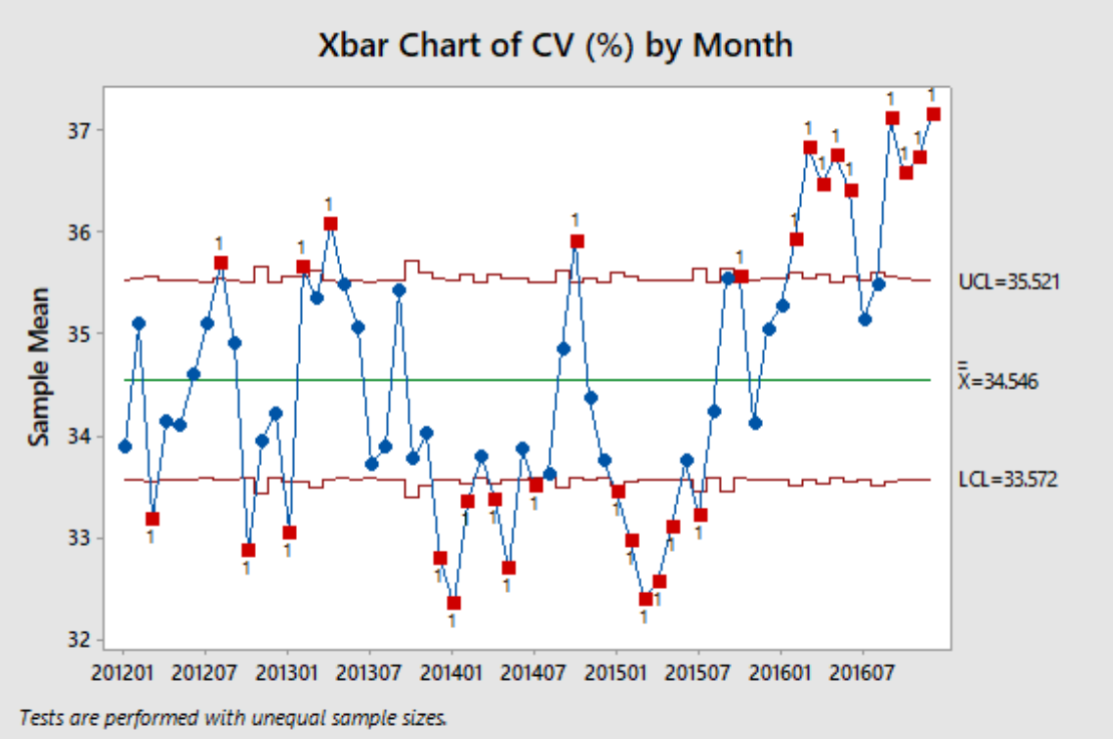
O KPI tem o coeficiente de variação (CV) no produto finalizado, mostrado aqui em uma carta Xbarra criada com o Minitab Statistical Software.
Com vários preditores interagindo entre si de maneiras complexas e infinitas, eles precisavam de uma abordagem organizada para identificar quais preditores afetavam mais a distribuição do tamanho da partícula. Eles precisam do TreeNet no Salford Predictive Modeler (SPM).
“Usar apenas técnicas de modelamento tradicionais foi difícil”, disse Russell. “Foi muito difícil para nós compreendermos as relações entre as variáveis e os resultados. Felizmente, o TreeNet do SPM facilitou muito para nós aperfeiçoarmos os preditores-chave e conseguir bolar estratégias para conseguir lidar com eles com eficácia. Acredito que o Minitab e o algoritmo do TreeNet do SPM podem trabalhar juntos muito bem e com eficácia. Certamente, o SPM não é um substituto para o Minitab ou outros programas de estatística, mas quando usados juntos, achamos que podemos conseguir uma resposta mais rápida.”
Russell usou as configurações padrão no TreeNet e ajustou o número de árvores. À medida que ele cortava os preditores, começou a compreender o efeito que isso tinha em comparação com um valor do R-quadrado.
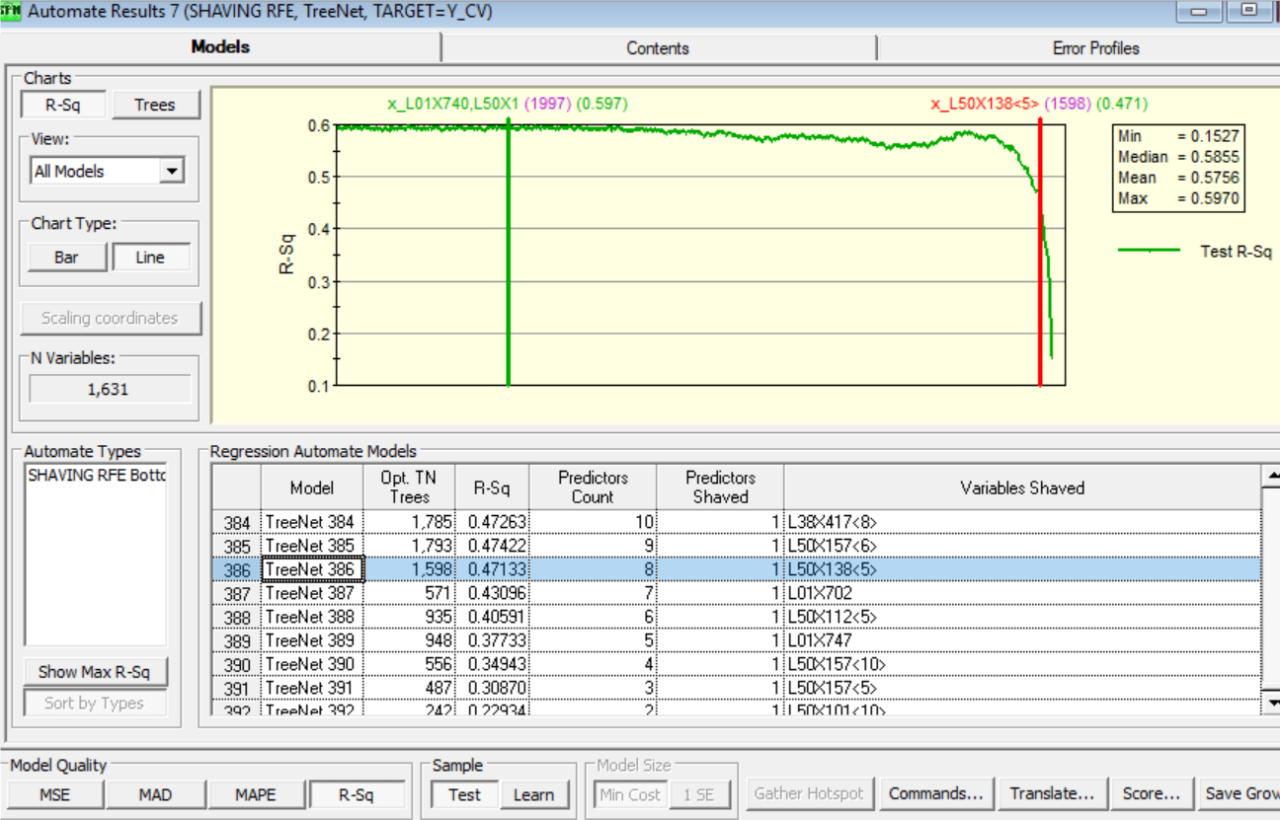
Este modelo para controle de tamanho de partícula tinha apenas 8 preditores, mas explica metade da variação na amostra de teste.
Para encontrar o verdadeiro significado por trás dessas variáveis críticas, Russell usou o gráfico de dependência parcial do SPM. Certas variáveis estavam caindo em locais íngremes na curva de dependência parcial, o que revelava sua importância. Sem a curva de dependência parcial do SPM, a importância dessas variáveis nunca seria encontrada.
Então, eles usaram uma abordagem direta e stepwise. Ele retirou uma variável por vez e observou o que acontecia com o R-quadrado. Ele não mudou significativamente até retirar a quarta variável mais importante. Essa variável foi levada à equipe de fabricação, com um pedido de mais informações.
Os resultados
Russell reduziu rapidamente mais de 1.000 preditores a apenas 8, usando a classificação de importância de variável do SPM. Esses 8 preditores foram responsáveis por quase metade da variação apenas nas amostras de teste.
Com o recurso “shaving desde cima”, Russell pôde ver rapidamente que uma variável teve um efeito significativamente maior no R-quadrado do que as outras variáveis. Descobriu-se que essa era a variável associada ao fluxo de alimentação do sistema de cristalização, mas seu impacto no produto final não foi compreendido claramente até que Russell criasse um modelo do SPM.
Depois, com os gráficos de dependência parcial do SPM, Russell conseguiu ver o motivo dessa variável ser tão importante na falta de confiabilidade do tamanho da partícula. Os gráficos de dependência parcial do SPM mostraram como essa variável poderia mudar em resposta às alterações em onde eles estavam “correndo na curva de distribuição”.
“Estamos correndo na parte mais íngreme dessa curva de distribuição”, disse Russell. “Em dias de sorte, o coeficiente de variação será baixo, mas em dias de azar, o coeficiente de variação será maior. Sem o SPM, nunca saberíamos disso.”
Satisfeito com a meta atingida, Russell encontrou algumas maneiras de reduzir a variação no tamanho final dos seus cristais de açúcar de milho e ajudou os fabricantes de alimentos a usar esses ingredientes para melhorar os produtos aos consumidores.
*Este estudo de caso foi criado com o Companion by Minitab, antes do lançamento do Minitab Engage em 2021.

O DESAFIO
Otimizar o processo de cristalização de açúcar com mais de 1.000 preditores interagindo entre si de maneiras complexas e infinitas para manter a distribuição do tamanho da partícula a mais uniforme possível.
PRODUCTS USED
Minitab® Statistical Software
Salford Predictive Modeler®
Minitab Engage®
COMO O MINITAB AJUDOU
A Tate & Lyle usou o Companion by Minitab* para criar um mapa de processo, o Minitab Statistical Software para compreender visualmente os dados de tamanho de partícula com uma carta Xbarra e o TreeNet no Salford Predictive Modeler para identificar quais preditores afetavam mais a distribuição do tamanho da partícula.
OS RESULTADOS
Eles descobriram 8 preditores que eram responsáveis por quase metade da variação. Durante os períodos de defasagem no processo, os operadores de fábrica poderia alterar o preditor com base nos suprimentos e fatores de demanda. Com essas informações, a Tate & Lyle descobriu maneiras de reduzir a variação no tamanho da partícula.