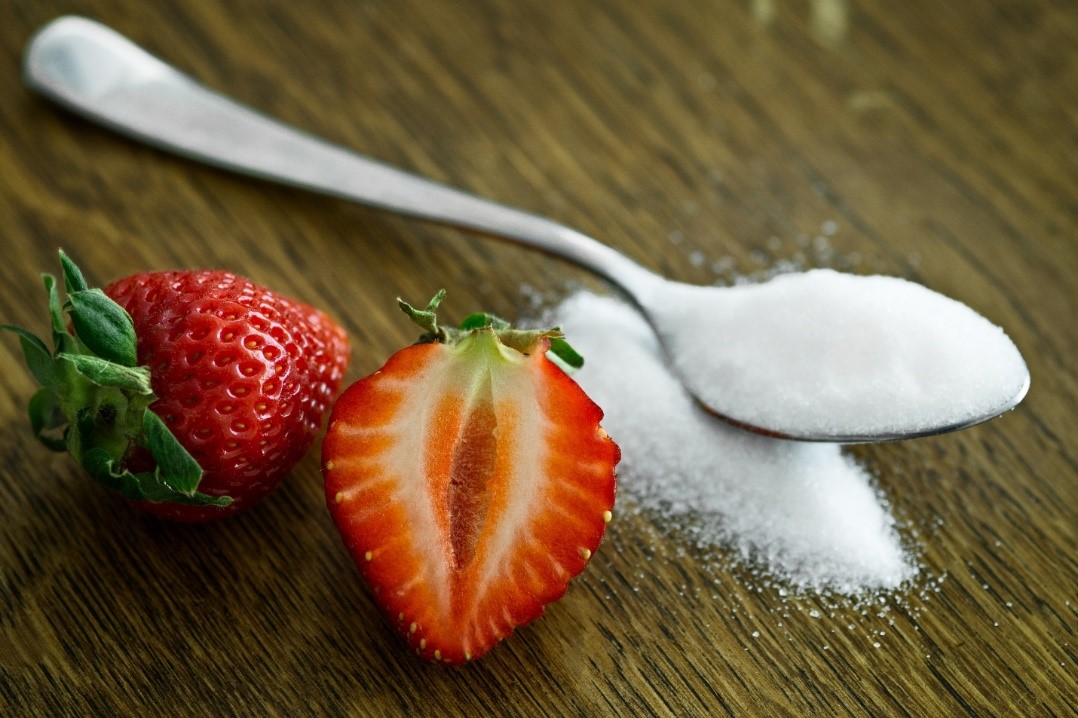
Tate & Lyleは、飲食料品業界のグローバル大手の一つであり、トウモロコシ、タピオカ、その他の原材料を、風味、食感および栄養素を付加する成分に変えて、長年にわたり「食品をすばらしいものとする」ことに目覚ましい業績をあげています。最もよく知られた同社の製品の一つは、SPLENDA®スクラロースという甘味料です。
Tate & Lyleは、コーンシュガーを生成する過程で課題に直面した際、Minitabのソフトウェアに支援を求めてきました。
その課題:結晶の粒度を均一にすること
アダム・ラッセルは、Tate & Lyleのグローバル・オペレーション・マスター・ブラック・ベルトとして職務を始めたとき、課題に直面しました。コーンシュガーの粒度を同一にするという課題です。
「結晶化プロセスの品質特性に決定的なものの一つは、粒度の分布です」とラッセルは言います。「なぜそれが問題となるのでしょうか。20~30年前にお客様のためにこれらの製品を開発した際、お客様は、コーンシュガーが通常のグラニュー糖や甘蔗糖と同じ風味や食感を有することを求めていました。そのような状態にするには、粒度が一定の分布の範囲内にある必要があります。」
Tate & Lyleは、許容範囲を逸脱する粒子に対処するという問題に直面しており、その理由を特定することができませんでした。同社は、粒度のばらつきに影響を与えると過去に判断した要素について、リストを有していました。
- 温度
- 圧力
- 流量
- pH
- 導電性
等々です。
Minitabによる支援方法
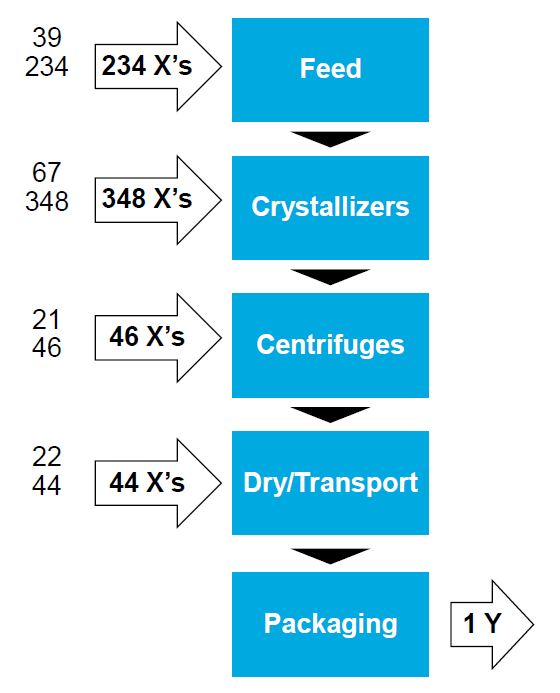
Tate & LyleがCompanion by Minitab (現行のMinitab Engage®) において作成したプロセスマップをシンプルにしたものです。コーンシュガーの結晶化のプロセスにおいて、シロップは精製装置から送り出され、それから結晶化され(数日かかる)、その後遠心分離され、乾燥され、最後に袋詰されます。
Companion by Minitab (現行のMinitab Engage®) を使用して、結晶化プロセスの俯瞰図を示すプロセスマップを作成することから始めました (プロセスマップの詳細についてはこちらをご覧ください)。彼らは、厳密な粒度分布を確保できていなかったため、何がばらつきを引き起こしているのか、そしてそれをどのように制御するのかを理解したかったのです。
「すべては、化学工場において測定されていました」と、ラッセルは言います。「可能な、あらゆる地点において、情報をデータ履歴担当者に提供するトランスミッタがありました。それはすばらしいことですが、私たちは情報過多となり、情報をどのように処理すればよいかわからないという課題が生じました。」
粒度データを視覚的に理解するため、ラッセルとそのチームは、 Minitab Statistical Software を使用して、下記に示す Xbar chart を作成しました。
ただし、変数間の関係の多くは非線形であるため、ある要素が他に与えた影響を特定するのは困難であることがわかりました。また、スクラロースは、「懸濁液」として知られる液体と固体の中間のゲル状の形で乾燥状態にあるため、袋詰めされるまで粒度は判明しません。
このようなモデルへのインプットには、1,000通り以上の可能性があります。重回帰モデル単独では答えにつながりませんでした
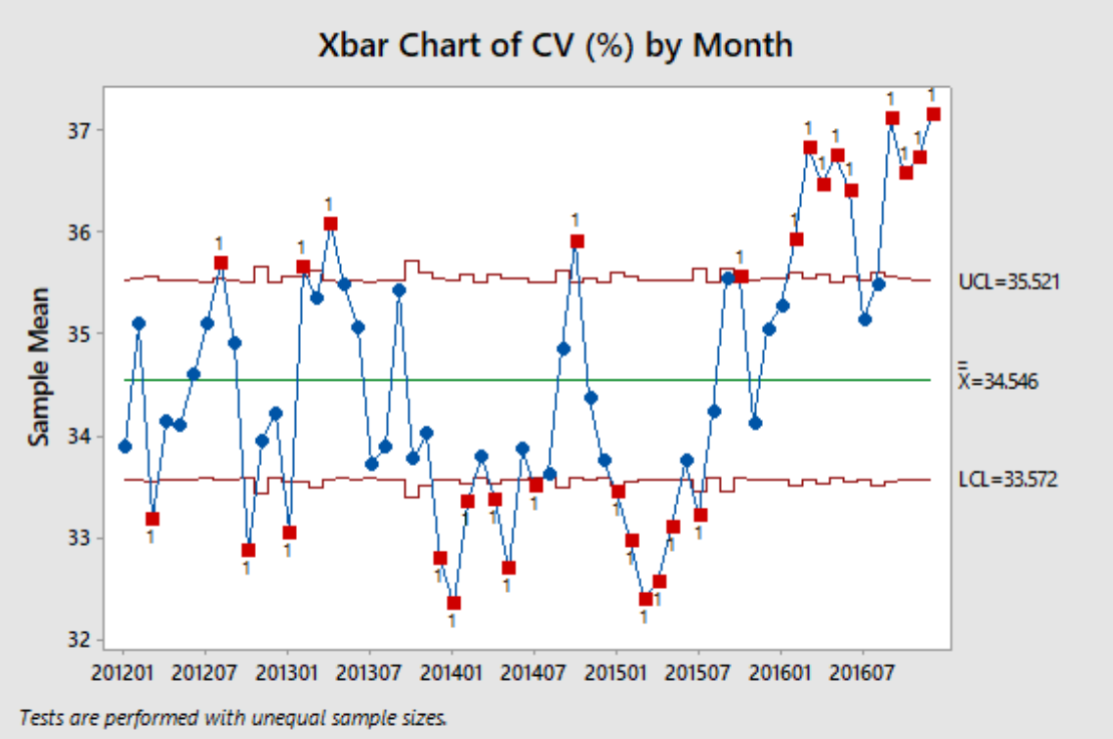
Key Process Indicatorは、最終製品の変動係数(CV)で、ここにある通り、Minitab Statistical Softwareで作成されたXbarチャートに表示されているものです。
多数の予測因子が無限に複雑な方法で相互作用するため、どの予測因子が粒度分布に最も影響を与えたかを特定する体系的なアプローチが必要でした。 TreeNet の Salford Predictive Modeler (SPM) を必要としていました。
「伝統的なモデル技術を使用するだけでは困難でした」とラッセルは述べます。「私たちにとって、変数と結果の間の関係性を理解するのは非常に困難でした。幸運にも、SPMのTreeNetによって、非常にシンプルに、重要な予測因子に焦点を合わせ、効果的に当該因子を扱う戦略を立案できるようになりました。私は、MinitabとSPMのTreeNetアルゴリズムが、非常に効果的に協働できると信じています。確かに、SPMは、Minitabやその他の統計プログラムの代替ではありませんが、一緒に使用すると、すぐにでも答えにたどりつくことができると思います。」
ラッセルは、TreeNetの既定設定を使用し、ツリーの数を調整しました。予測因子を削り始めるにつれて、彼は、当該因子が決定係数の試験値に及ぼす影響を理解し始めました。
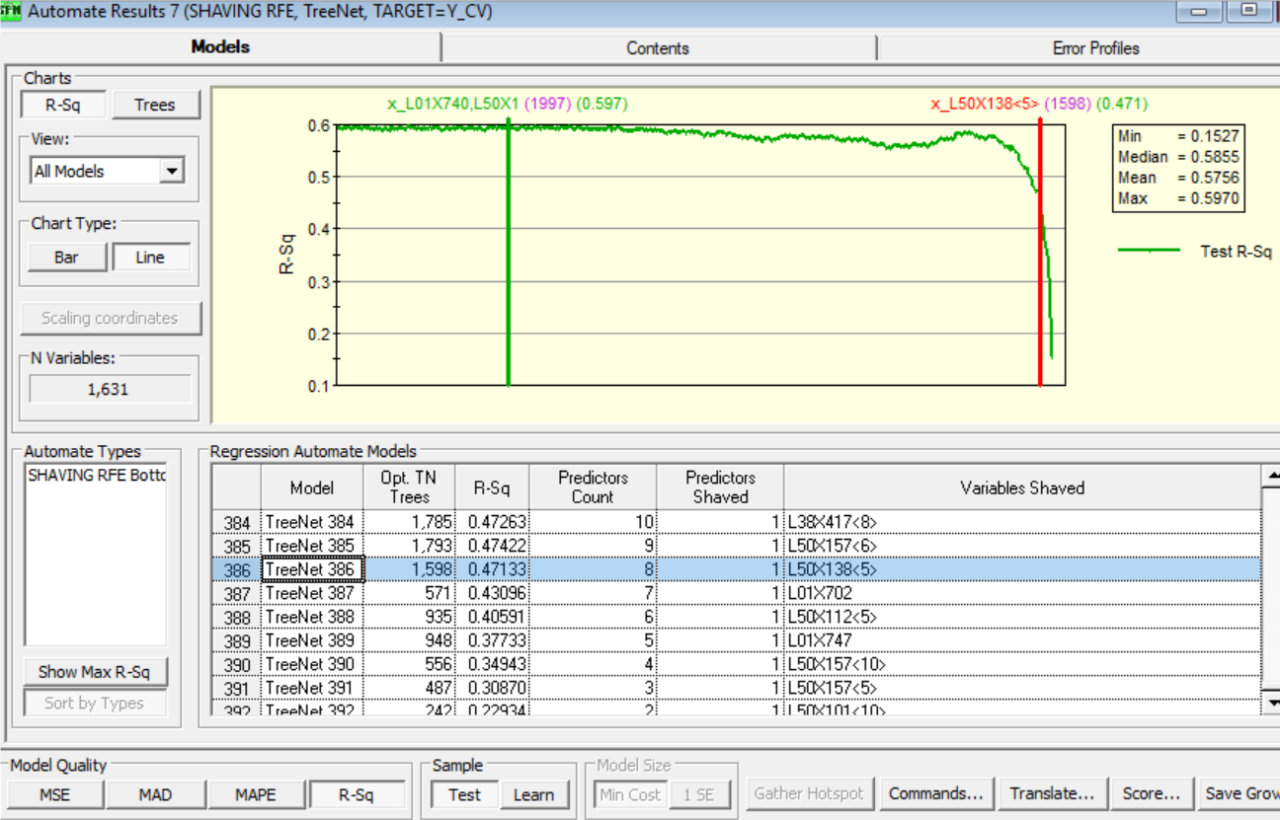
粒度制御の本モデルには、8つの予測因子しかありませんが、テストサンプルにおけるばらつきの半分が説明できます。
ラッセルは、これらの決定的な変数の背景にある真の意味を見出すために、SPMの部分従属プロット(partial dependency plot)を使用しました。特定の変数は、偏依存曲線上の急勾配の位置にあり、それが重要であることが明らかになりました。SPMの偏依存曲線がなければ、これらの変数の重要性は決して見出されることはなかったでしょう。
その後、彼は、直接的かつ段階的なアプローチを採用しました。彼は、一度に1つずつ変数を取り出し、決定係数に何が起こるのかを観察しました。4番目に最重要な変数を取り出すまでは、顕著な変化はありませんでした。彼は、この変数を製造チームに持っていき、それに関してより多くの情報を提供するよう求めました。
結果
ラッセルは、SPMの変数重要度ランキングを用いて、1000以上の予測因子を速やかにたった8つにまで絞り込みました。そして、これらの8つの予測因子は、テストサンプルにおけるばらつきのおおよそ半分の原因を成すものでした。
ラッセルは、SPMの「トップから削る(shaving from the top)」という機能を用いて、迅速に、ある一つの変数が他のどの変数よりも決定係数に著しく大きな影響を及ぼしていることを観察することができました。これは、結晶化システムへの供給流に関連する変数であることが判明しましたが、ラッセルがSPMモデルを作成するまで、最終製品に対するその影響は明確には理解されていませんでした。
その後、SPMの部分従属プロットを用いることによって、ラッセルは、なぜこの変数が粒度の信頼性の低さにおいて非常に重要であるかを理解することができました。SPMの部分従属プロットは、当該変数が「分布曲線上の配置」場所の変化に応じて、どのように変化する可能性が高いかを示しました。
「この分布曲線の急勾配の部分に配置されていました」とラッセルは述べています。「運の良い日は変動係数は低いままですが、運の悪い日は、変動係数は高くなります。SPMがなければ、私は決してそれを知ることはありませんでした。」
ラッセルは、彼の目標が達成されたことに満足しました。そして、同社のコーンシュガー結晶の最終的な粒度のばらつきを減らし、消費者のために同社の製品を改良して、食品メーカーが同社の調味料を使うのを助けることができるいくつかの方法を見つけました。
*このケーススタディは、2021年にMinitab Engageが導入される前に、Companion by Minitabを使用して作成されました。

課題
無限に複雑な方法で相互作用する1000以上の予測因子を伴うコーンシュガーの結晶化プロセスを最適化し、粒度分布をできる限り均一に保持すること。
PRODUCTS USED
Minitab® Statistical Software
Salford Predictive Modeler®
Minitab Engage®
MINITABによる支援方法
Tate & Lyleは、Companion by Minitabを使用してプロセスマップを作成し、 Minitab Statistical softwareを使用して、Xbar chartとともに粒度データを視覚的に理解し、Salford Predictive ModelerのTreeNetを使用して粒度分布に最も影響を与える予測因子を特定しました。
結果
彼らは、8つの予測因子が、ばらつきのおよそ半分の原因を成すものであることを発見しました。プロセスの遅滞期中に、プラントオペレータは需要と供給の要因に基づいて予測因子を変更する可能性があります。この情報を武器として、Tate & Lyleは、粒度のばらつきを減らす方法を見出しました。