O mundo adora uma boa cerveja. O consumo anual aumentou por 28 anos consecutivos para mais de 193 bilhões de litros. As cervejarias artesanais americanas reivindicam uma parte crescente desse mercado. Em apenas um ano, elas abriram 615 novas cervejarias e aumentaram a produção em 18%.
A Anheuser-Busch InBev tem acompanhado essa tendência, expandindo suas ofertas além das famosas cervejas Budweiser e Bud Light para incluir mais de 200 marcas.
Porém, a produção de uma grande variedade de cervejas foi desafiadora e a empresa notou que seu resultado financeiro estava sendo limitado por atividades de interrupção planejadas, como o processo inicial e alterações de marca necessários para produzir todas essas bebidas. E essas interrupções planejadas aumentavam, conforme o número de marcas crescia.
Usando o Minitab para analisar seus dados, uma equipe dedicada conclui um projeto Lean Six Sigma que não só reduziu as interrupções planejadas e economizou dinheiro, como também forneceu uma solução que a empresa poderia distribuir globalmente para multiplicar o sucesso do projeto.
O desafio
A equipe de projeto, que incluía partes interessadas e participantes de todos os níveis da empresa, decidiu visar algumas cervejarias piloto. Eles definiram como meta, reduzir a inatividade em 30% e os custos em US$ 200.000. A equipe identificou benefícios adicionais que esperavam ver, como redução no consumo de energia e maior envolvimento de operadores.
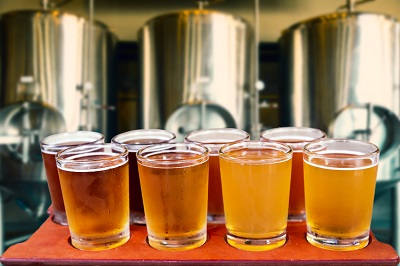
Como a empresa não tinha nenhuma abordagem formal para reduzir a inatividade, a equipe também queria criar um kit de ferramentas que poderia ser usado globalmente para replicar os ganhos do projeto. Para garantir que seu kit de ferramentas fosse eficaz, eles planejaram sondar os operadores sobre a facilidade de compreensão e aplicação dos materiais e desejaram obter uma pontuação média de pelo menos 4,5 de 5.
Como o Minitab ajudou
Não é possível resolver um problema antes de compreendê-lo. Para identificar as causas das interrupções, a equipe reuniu meticulosamente uma grande matriz de dados. Eles mapearam o processo em detalhes e documentaram fluxos de tarefas separadas para cada operador. Eles anotaram a quantidade de desperdício que observaram e registraram o tempo que levou para cada funcionário da linha de produção concluir até mesmo as menores ações, como colocar as luvas e pegar suas ferramentas.
Eles usaram um conjunto igualmente amplo de ferramentas do Minitab para analisar o estado dos dados reunidos, incluindo gráficos de Pareto para identificar os maiores contribuintes para as interrupções, histogramas para compreender o comportamento do processo e cartas de controle e outros gráficos para comparar vários turnos e cervejarias.
Eles também usaram o Assistente do Minitab, que ajuda a escolher as análises corretas e fornece relatórios abrangentes, para conduzir uma ANOVA e comparar médias. Usando teste de hipóteses, eles determinaram que havia diferenças significativas na maneira que turnos diferentes executavam o processo.
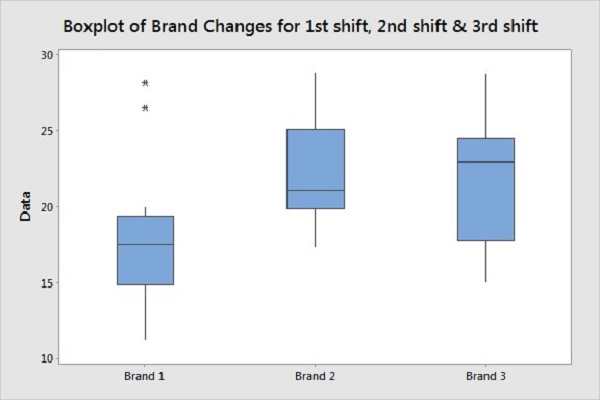
Obter um panorama só com os números é difícil, portanto, a equipe usou os boxplots do Minitab e outros gráficos para visualizar as diferenças no desempenho das alterações de marca em vários turnos.
Obter um panorama só com os números é difícil, portanto, a equipe usou os boxplots do Minitab e outros gráficos para visualizar as diferenças no desempenho das alterações de marca em vários turnos.
Como parte da análise de causa principal, eles também usaram R&R da medição para conduzir análise de sistemas de medição para garantir que suas medições eram confiáveis, antes de tentar qualquer melhoria. A análise levou à conclusão de que os indicadores de disco e os tempos do processo não eram confiáveis e precisavam ser tratados.
Graças à grande perspicácia para os detalhes e o poder de análise do Minitab, a equipe conseguiu identificar as causas principais do tempo excessivo de interrupção, que incluía um procedimento de operação padrão para conversão de linha que estava longe do ideal e diferenças significativas em como os turnos executavam o processo. Ele descobriram também que esses problemas eram consistentes em todas as instalações e processos.
Eles precisavam então descobrir uma solução que pudesse ser transferida.
Para determinar como o processo deveria ser ajustado, a equipe fez um brainstorm de ideias, mapeou-as de volta às causas de origem e classificou-as de acordo com o impacto e dificuldade. Depois, eles classificaram suas ideias em todas as instalações e processos para confirmar melhor sua viabilidade.
A lista final de soluções incluía a otimização do processo de conversão através da simplificação e automação de tarefas e redução do procedimento atual de interrupção, que continha 30 páginas e não era prático, para uma lista de verificação de 1 página. Eles também planejaram oferecer treinamento consistente aos operadores de linha e adicionaram um timer de LED no piso para fornecer uma informação precisa sobre a interrupção e criar uma sensação de urgência.
Para validar essas soluções, a equipe criou um plano detalhado para executar um teste piloto em pequena escala e projetou o impacto que as soluções teriam nas metas originais. Só a preparação para a implantação desencadeou grandes melhorias no envolvimento dos operadores. Os diversos turnos ficaram empolgados em ver que podiam fazer a diferença e estavam até se preparando para competir pelos melhores tempos.
Resultados
A implantação dos procedimentos melhorados nas avaliações superou as expectativas da equipe. As melhorias reduziram o tempo de inatividade planejado em 34% e os custos relacionados em mais de US$ 430.000. Um tempo de inatividade menor significou que o processo de conversão exigia menos energia, fornecendo mais economias.
A equipe também viu uma melhoria de quase 40% no tempo que levou para retomar a produção, o que amplificou seus ganhos. As cartas de controle do Minitab confirmaram as mudanças positivas e foram usadas para estabelecer limites para garantir que os resultados fossem mantidos ao longo do tempo.
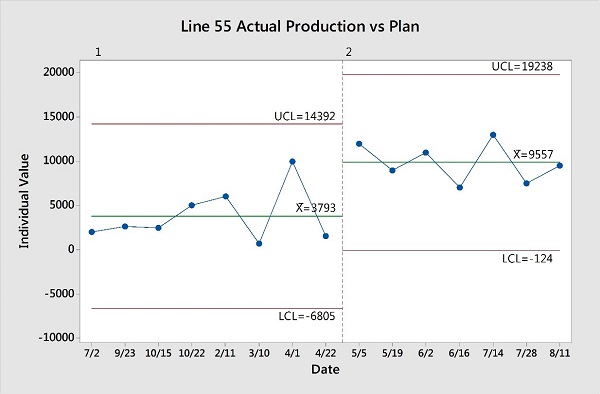
As cartas de controle do Minitab foram usadas para estabelecer limites e garantir que os resultados fossem mantidos no futuro.
As alterações feitas pela equipe foram fáceis de combinar em um kit de ferramentas que outras instalações e processos poderiam adotar. Os operadores adotaram a lista de verificação e outros procedimentos que economizavam tempo e deram à eficácia do kit de ferramentas uma avaliação média de 4,85 em 5. Os resultados da sondagem também indicaram que os operadores estavam mais envolvidos em seu trabalho, especialmente quando perguntados se seu trabalho fazia alguma diferença.
Esses resultados deram a confiança à equipe de que eles poderiam distribuir o kit de ferramentas ampla e eficazmente, o que foi exatamente o que fizeram. O kit de ferramentas foi aplicado a dezenas de milhares de processos em mais de 180 instalações em todo o mundo, criando um sucesso exponencial.
Reunir os dados sobre o processo de interrupção de atividades e analisá-los com o Minitab teve um impacto direto e duradouro na capacidade da Anheuser-Busch InBev de produzir de maneira barata a grande variedade de cervejas que seus clientes desejam, e isso é uma realização que pode ser brindada por todos aqueles que apreciam qualidade e eficiência.
Esse estudo de caso é baseado na apresentação que a Anheuser-Busch InBev enviou à competição do International Team Excellence Award da ASQ em 2014. A apresentação está disponível aos membros da ASQ e a inscrição é gratuita. Baixe a apresentação da Anheuser-Busch InBev.
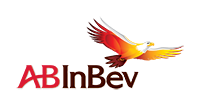
ORGANIZAÇÃO
Anheuser-Busch InBev
VISÃO GERAL
- A maior empresa de cerveja com operações em 25 países
- 155.000 funcionários e mais de 200 marcas de cerveja
- Receita de US$ 47 bilhões
DESAFIO
Reduzir o tempo de interrupção da linha de produção para atender à procura dos clientes por maior variedade de cervejas.
PRODUTOS USADOS
Minitab® Statistical Software
RESULTADOS
- Tempo de interrupção reduzido em 34%
- Custos com tempo de interrupção reduzidos em mais de US$ 430.000
- Criação de um kit de ferramentas para aplicar melhorias em mais de 180 instalações