La bière est une boisson en vogue. Après 28 années consécutives d'augmentation, la consommation annuelle mondiale atteint aujourd'hui 193 milliards de litres. Les brasseries artisanales américaines se partagent une part croissante sur le marché avec l'ouverture de 615 brasseries en un an et une augmentation de 18 % de la production.
Surfant sur la tendance, Anheuser-Busch InBev a acquis de nouvelles brasseries et compte désormais plus de 200 marques dont les célèbres Budweiser et Bud Light.
Mais avec la production d'une grande variété de bières, l'entreprise a constaté que les activités impliquant des temps d'arrêt planifiés, comme le changement de marques nécessaires pour produire les boissons, avaient un impact sur ses bénéfices. Et plus l'entreprise acquiert de nouvelles marques, plus les temps d'arrêt planifiés augmentent.
Une équipe a mené à bien un projet Lean Six Sigma en utilisant Minitab pour analyser les données. Ce projet a permis non seulement de réduire les temps d'arrêt planifiés et de réaliser des économies, mais également de créer une solution que l'entreprise peut mettre en oeuvre à l'échelle mondiale.
La problématique
L'équipe de projet, dont les membres incluaient des parties prenantes et des participants issus de chaque niveau de l'entreprise, a décidé de cibler plusieurs brasseries pilotes. Leur objectif était de réduire les temps d'arrêt de 30 % et les coûts de 200 000 $. L'équipe avait identifié d'autres résultats potentiels qu'elle espérait atteindre, notamment la réduction de la consommation d'énergie et une implication accrue des opérateurs de la ligne de production.
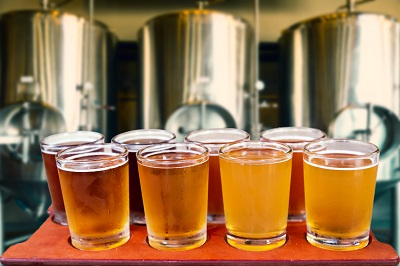
Etant donné qu'aucun processus officiel de réduction des temps d'arrêt n'avait été mis en place, l'équipe souhaitait également créer une trousse à outils qui pourrait être utilisée à l'échelle mondiale pour reproduire les excellents résultats du projet. Pour tester l'efficacité de leur trousse à outils, les membres de l'équipe ont demandé aux opérateurs d'évaluer la convivialité et la simplicité des outils. Ils visaient une note moyenne d'au moins 4,5/5.
La contribution de Minitab
Pour résoudre un problème, il faut en comprendre les origines. Pour identifier les causes profondes des temps d'arrêt, les membres de l'équipe ont collecté avec minutie un ensemble de données. Ils ont élaboré un processus détaillé et ont consigné les flux de tâches distincts pour chaque opérateur. Ils ont noté la perte de temps constatée ainsi que le temps nécessaire à chaque opérateur pour exécuter chacune des actions, même les plus insignifiantes comme enfiler ses gants et sortir ses outils.
Ils ont utilisé les outils Minitab pour analyser la myriade de données collectées, notamment des diagrammes de Pareto pour identifier les principales sources des temps d'arrêt, des histogrammes pour comprendre le comportement du processus, et des cartes de contrôle ainsi que d'autres graphiques pour comparer les différentes équipes et brasseries.
Ils ont également utilisé l'Assistant de Minitab, qui aide à choisir le processus d'analyse approprié et fournit des rapports détaillés, pour effectuer une analyse de la variance et comparer les moyennes. A partir de tests d'hypothèse, ils ont mis en évidence des différences significatives dans la manière dont les différentes équipes exécutaient le processus.
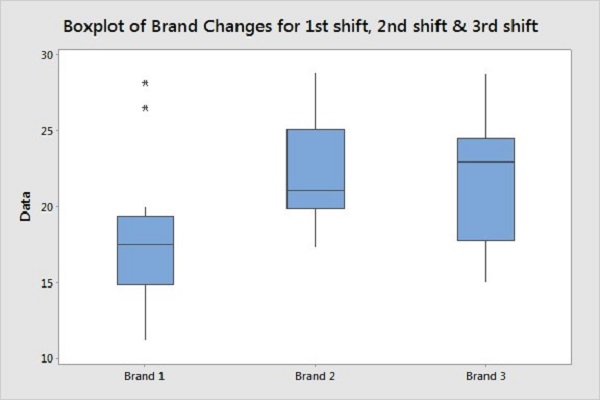
Parce qu'il est compliqué d'interpréter un résultat uniquement à partir de chiffres, l'équipe a utilisé les boîtes à moustaches et d'autres graphiques dans Minitab pour visualiser les différences dans la manière dont les différentes équipes exécutent le processus de changement de marque.
Parce qu'il est compliqué d'interpréter un résultat uniquement à partir de chiffres, l'équipe a utilisé les boîtes à moustaches et d'autres graphiques dans Minitab pour visualiser les différences dans la manière dont les différentes équipes exécutent le processus de changement de marque.
Dans le cadre de l'analyse des causes principales, ils ont réalisé une étude R&R de l'instrumentation pour analyser les systèmes de mesure afin de vérifier leur fiabilité avant de tenter d'appliquer une quelconque amélioration. L'analyse a révélé un manque de fiabilité au niveau des comparateurs à cadran et de la synchronisation du processus.
Grâce à son coup d'oeil scrutateur et à la puissance d'analyse de Minitab, l'équipe a réussi à identifier les causes profondes des temps d'arrêt excessifs, à savoir une procédure standard de conversion des lignes loin d'être optimale et des différences significatives dans la manière dont les différentes équipes exécutent le processus. Ils ont également déterminé que ces problèmes concernaient toutes les usines et tous les processus.
Il leur fallait ensuite développer une solution qui soit transférable.
Pour déterminer comment ajuster le processus, l'équipe a mis en commun ses idées, les a mises en rapport avec les causes principales et a évalué leur impact et difficulté. Ils ont ensuite classé leurs idées selon les usines et processus pour valider leur viabilité.
La liste définitive de solutions incluait la rationalisation et l'automatisation des tâches pour optimiser le processus de conversion, et la simplification de la liste de contrôle des temps d'arrêt actuelle beaucoup trop contraignante en réduisant les 30 pages qui la composent à une seule page. Ils ont recommandé que tous les opérateurs suivent une formation cohérente et ont ajouté une minuterie à LED pour fournir des informations précises sur les temps d'arrêt et créer un sentiment d'urgence.
Pour valider ces solutions, l'équipe a élaboré un programme détaillé visant à les tester sur une petite échelle et a réalisé des prévisions de leur impact sur les objectifs initiaux. La phase de préparation de la mise en oeuvre a eu un impact non négligeable sur l'implication des opérateurs. Chaque équipe était impatiente de tester sa capacité à s'améliorer et à surpasser les autres équipes.
Résultats
Les résultats de la mise en oeuvre des améliorations dans les brasseries pilotes ont surpassé les attentes de l'équipe. Les améliorations ont permis de réduire les temps d'arrêts de 34 % et les coûts associés de plus de 430 000 $. La réduction des temps d'arrêt a eu un impact sur la consommation d'énergie du processus de conversion, ce qui a généré une économie supplémentaire.
L'équipe a également constaté une amélioration de près de 40 % du temps nécessaire pour relancer la production, permettant ainsi à l'entreprise d'accroître ses bénéfices. Les cartes de contrôle de Minitab ont confirmé l'impact positif sur les équipes. Elles ont également servi à établir des limites et à garantir la pérennité des résultats.
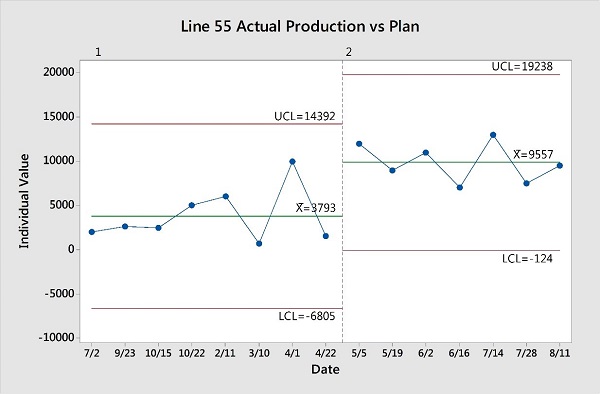
Les cartes de contrôle de Minitab ont été utilisées pour établir des limites et garantir la pérennité des résultats.
Les changements apportés par l'équipe ont été facilement intégrés à une trousse à outils réutilisable dans les autres usines et pour d'autres processus. Les opérateurs ont adopté la nouvelle liste de contrôle ainsi que les autres procédures visant à gagner du temps, et ont donné la note moyenne de 4,85/5 à la trousse à outils. L'enquête a également révélé que les opérateurs s'impliquaient davantage et appréciaient particulièrement l'amélioration des performances de leurs tâches quotidiennes.
L'ensemble de ces résultats a conforté l'équipe dans l'idée que la trousse à outils était efficace et qu'elle pouvait être distribuée à grande échelle, ce qui a été fait. La trousse à outils a été appliquée à des dizaines de milliers de processus dans plus de 180 usines à travers le monde pour reproduire les résultats du projet pilote.
La collecte de données sur les temps d'arrêt et l'analyse de celles-ci dans Minitab a eu un impact direct et durable sur la capacité d'Anheuser-Busch InBev à produire une grande variété de bières grâce à un processus fiable, performant et économique.
Cette étude de cas est basée sur la présentation transmise par Anheuser-Busch InBev à l'American Society for Quality (ASQ) dans le cadre du concours International Team Excellence Awards 2014. La présentation est disponible pour les membres de l'ASQ ; l'inscription est gratuite. Téléchargez la présentation Anheuser-Busch InBev.
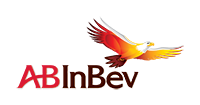
Organisation
Anheuser-Busch InBev
Présentation
- Brasseur leader dans le monde présent dans 25 pays
- 155 000 employés et plus de 200 marques de bière
- Chiffre d'affaires de 47 milliards de dollars
Le défi
Réduire les temps d'arrêt sur la chaîne de production pour offrir aux clients une plus grande variété de bière.
Produits utilisés
Minitab® Statistical Software
Résultats
- Réduction des temps d'arrêt de 34 %
- Réduction des coûts associés aux temps d'arrêt de plus de 430 000 $
- Création d'une trousse à outils pour la mise en place des améliorations dans plus de 180 usines