Based in Königswinter, Germany, Maxion Wheels is one of the most reputable and trusted companies in the vehicle parts manufacturing industry. The organization, founded in 1908, is the world’s largest wheel producer and is striving to become the first carbon-neutral manufacturer in the market.
As a worldwide organization with workers from many different backgrounds, Maxion Wheels continuously has over fifteen hundred major projects in progress. Their initiatives range from operational excellence, continuous improvement, engineering, CAPEX, supply chain, IT and innovation projects.
Emine Uslu is a Regional Operational Excellence Manager at Maxion Wheels and oversees their operational excellence project management. For the past several years, Emine sought to improve visibility, increase cost savings, and pass value on to their customers.
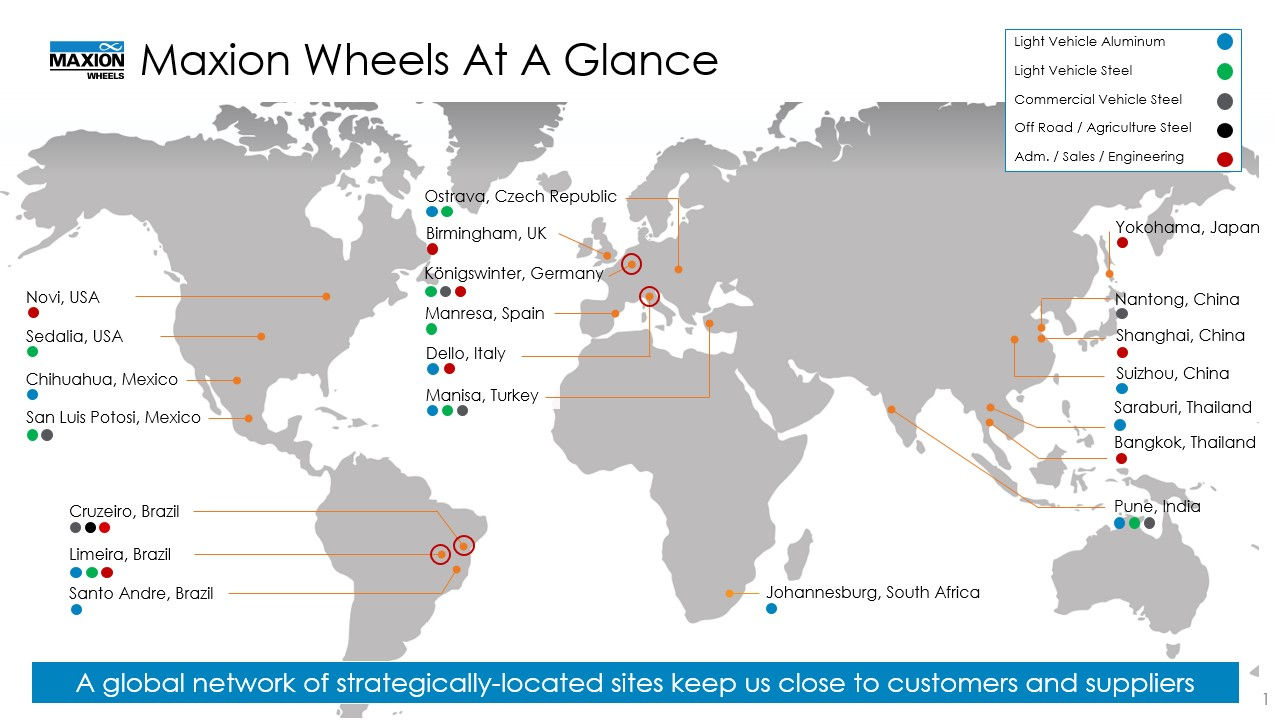
Maxion Wheels has plants and locations all around the world.
The Challenge
Maxion Wheels did not have a digital platform to provide instant insight into continuous improvement and operational excellence projects.
Prior to 2018, Maxion Wheels used spreadsheets to track project management and execution.
This situation stymied progress and created a gap between when information was retrieved and when it was presented. Company leaders were not getting the most up to date information which prohibited timely and data-driven decision making. Additionally, spreadsheets were tedious to manage and maintain.
The company utilized Project Charter templates that were in Excel, and they were not standardized for all functions or the whole company. There was no ubiquitous platform for sharing all projects.
Teams were using various types of metrics to track savings and different methods and tools to monitor KPIs. This was generally done in Excel with numerous formats that could not be compiled nor reconciled.
There were no up-to-date reports. Manual work was needed after data collection in Excel to build reports that were prone to errors.
As a result, the World Leader in Wheels decided to enact change.
The company needed to find a method to gain instant visibility and access to project dashboards to offer consistent and useful metrics for all stakeholders. Most critically, Maxion Wheels wanted to find more efficient ways to reduce waste to turn cost savings over to their customers. Additionally, they sought standardization and wanted to have an end-to-end platform for project and program management.
The Solution
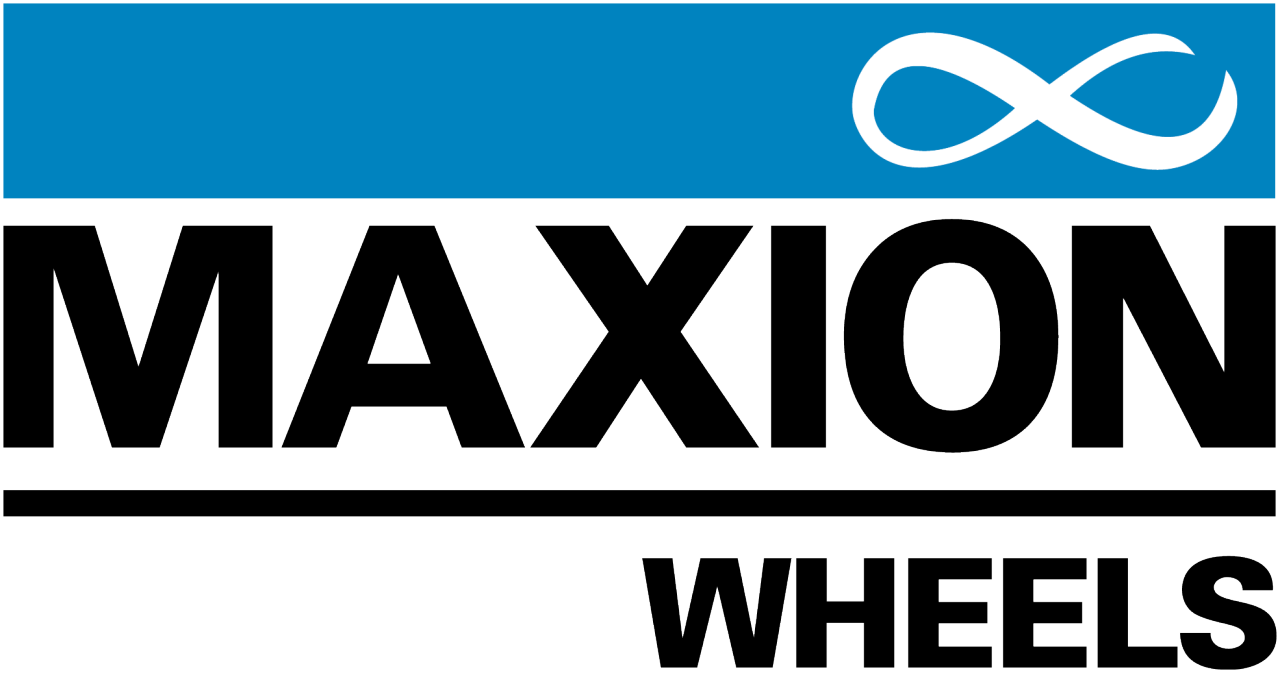
The Organization
Maxion Wheels
The Challenge
Due to difficulties in accessing project data and standardizing templates, Maxion Wheels sought to implement a digital platform for tracking continuous improvement projects.
Products Used
Minitab® Statistical Software
Minitab Engage®
The Solution
Maxion Wheels deployed Minitab Engage for centralized project management, standardized templates and real-time updates, resulting in increased productivity and collaboration.
The Results
Maxion Wheels currently manages 1,600 projects with Engage.
Minitab Engage helped to boost Maxion Wheels' annual savings from 6.8% to 8.1%.
Maxion Wheels achieved a drastic increase in total hard savings after adopting Minitab Engage.