Newcrest Mining Limited is one of the world’s top 10 gold mining companies and Australia’s largest gold producer. Newcrest’s Cadia Hill mine, the second-largest open pit gold-copper mine in Australia, produces approximately 300,000 ounces of gold annually. But its low-grade ore requires costly bulk mining and treatment techniques. Newcrest applies the Six Sigma quality improvement methodology and Minitab® Statistical Software to keep the Cadia Hill facility running as efficiently as possible, and to safeguard their prominent role in the gold industry.
The Challenge
Many times per day, a fleet of large haul trucks descends a narrow ramp to the bottom of the Cadia Hill open pit, where each truck picks up an average of 225 tons of ore to carry back up the ramp to a crushing machine for processing. The speed of the loaded trucks ascending the single-lane ramp varies from 8 to 14 kilometers per hour. Slower trucks, of course, take longer to deliver their payloads to the crusher. Even worse, each slow truck delays all the trucks behind it, hampering the performance of the entire fleet and resulting in a serious loss of productivity. Newcrest Mining tasked Six Sigma Black Belt James Kovac to reduce that variability and increase the average speed of the ascending trucks.
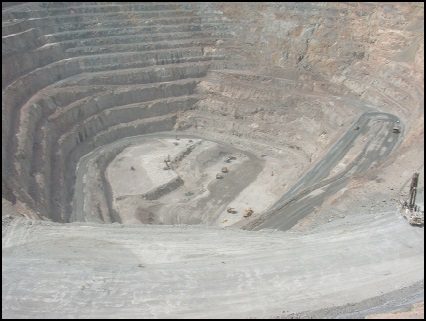
With Minitab Statistical Software, Newcrest Mining can get an additional load of ore per truck each day from its Cadia Hill mine.
How Minitab Helped
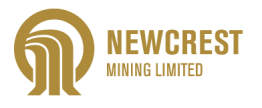
Organization
Newcrest Mining Limited
Overview
- Australia’s largest gold producer
- Over 4,500 employees and long-term contractors
- World’s most successful discoverer of major gold deposits, 1992–2005
Products Used
Minitab® Statistical Software
Results
- Quantified factors with greatest impact on haul truck speed
- Adjusting ramp grade improved haul speeds by 2.6%
- Project will save more than $835,000 in just its first year